With seven different machinery groups, seventeen types of machines, and over 50 machines, of which 35 are brand new, we have a wide variety of options to offer the most appropriate, fastest, and most cost-efficient production methods for our customers’ bespoke cut and converted products.
Technologies
Flat-bed cutting
FlatBed machines are a group of flatbed punching machines.
These machines in their factory state are suitable for conversion from rolls. The operating principle of the machines is that a tool is mounted above the material and cuts onto a precision steel plate (or anvil).
FlatBed converting machines are suitable for the production of both simpler shapes or complex layered products, cut in several steps, with or without fingerlift. It is possible to remove the internal waste.
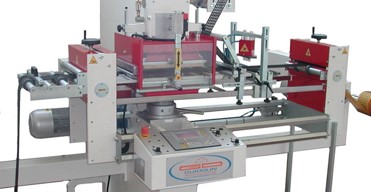
Rotary
Converting equipment that works on the rotary knife cutting principle and can be built in a modular manner.
The main steps of Rotary technology:- Lamination
- Liner removal, liner replacement (if needed)
- Cutting to the required shape
- Waste removal on the machine
- Rewinding / cutting to sheet presentation.
These machines can be equipped with a camera system to enable very accurate size and quality control.
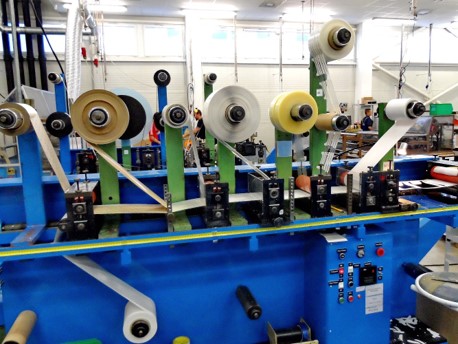
Hybrid
The Sysco machines use rotary and rotary+laser cutting technology.
- Produce multi-layer complex products in one pass.
- Highest accuracy and precision available.
- Converting, laminating, rotary die cutting and laser cutting.
- Each station is driven by a servomotor, which communicates with any others being used and makes automatic adjustments.
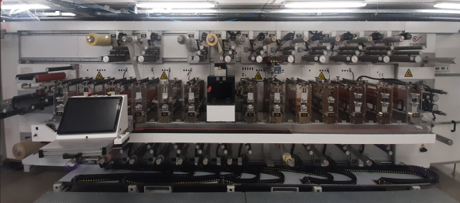
Press
Press machines are a group of flatbed punching machines that include Swing Beams, Crosslands, Beam presses, Guillotines and manual rewinders. They have different workspaces.
General rules and limitations:
- The tool is placed on a flat sheet and cut onto a precision steel plate.
- All Flat-bed tools can be used on the machines in the Press section, offering extra flexibility.
- Waste removal on all these machines is only possible manually.
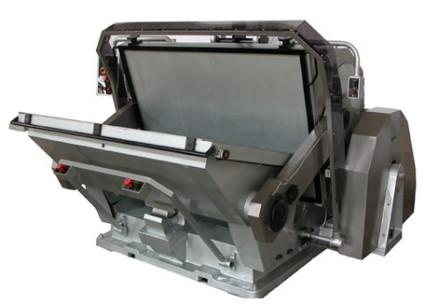
Laser
The majority of custom-made components are manufactured by either flat-bed or rotary tools. However, laser cutting is an option to overcome some of the limitations of the other cutting technologies.
These include:
- excessive thickness or hardness of the material
- a distance of less than 1.5 mm between any two blades of the tool.
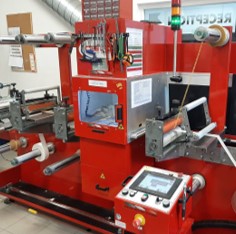
Thermoforming
Forming thermoplastic materials with a tool into the desired 3D shape. During thermoforming, the raw materials are heated and a 3D shape is created from the flat raw material with a tool.
Thermoformed products acquire their final form through the following steps:
- Preparation, raw material sheet cutting with traditional technologies.
- Sufficient heating of the raw material.
- Forming with dedicated tools.
- Removal of excess material on moulded products.
- Cutting of the edges and internal holes on products (with a tool or a laser).
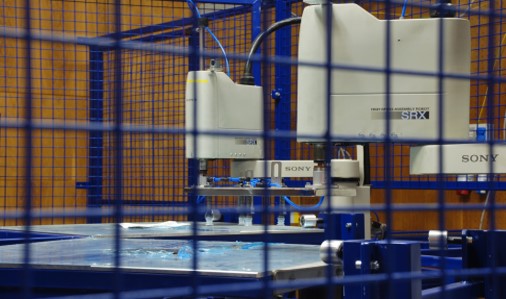
Slitting
In the case of approximately 85% of our productions slitting is what we call, the zero-technological step.
The chosen roll presented raw materials are cut to the requested width slits on either one of the Cevenini machines or on the Qualirolls. The slit type of products are also produced on these cutting machines.
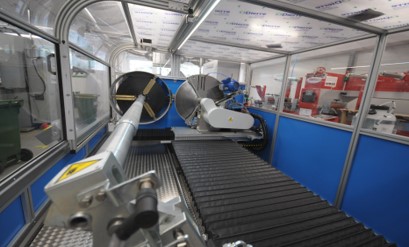
Cleanroom
Our ISO Class 7 Cleanroom can be utilised for converting parts for biotechnology, pharmaceutical, nanotechnology, and various cleantech manufacturing applications, such as:
- ion lithium batteries,
- driving radar sensors,
- medical devices,
- optically clear adhesives,
- aerospace products.
Depending on the product a dedicated machine can be placed in the Clean Room, if necessary.
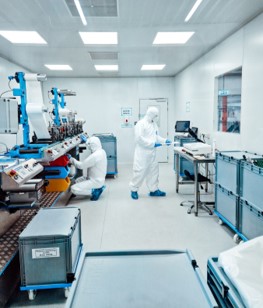